The VT1000 is a specialized technological device widely recognized for its robust performance in various industrial settings. Its capabilities are particularly notable in subzero environments, such as those encountered in liquefied natural gas (LNG) operations. This article provides a comprehensive analysis of the VT1000’s design, functionality, and application within the harsh conditions of a subzero LNG environment. By exploring its dimensions, installation requirements, performance challenges, and real-world applications, we aim to offer an in-depth understanding of this critical piece of equipment.
The VT1000: A Technological Overview
To understand how the VT1000 performs in a subzero LNG environment, it’s crucial to first grasp its general characteristics and functionalities. The VT1000 is designed to meet the rigorous demands of industrial applications, often involving VT1000 in Subzero LNG Environment data collection, monitoring, or control systems. Its design integrates advanced technology aimed at ensuring reliability, precision, and durability.
Design and Construction
The VT1000’s design is tailored to endure harsh operating conditions. This includes the use of high-quality materials that resist wear and tear, extreme temperatures, and other environmental stresses. The device typically features a sturdy housing that protects its internal components from physical damage and environmental hazards. In the context of subzero LNG environments, the device’s construction must address the specific challenges posed by extremely low temperatures.
Functionality
The VT1000 is engineered for precision and efficiency, making it suitable for various industrial applications. It can perform functions such as real-time monitoring, data logging, and automated control, depending on its configuration. In LNG environments, these functionalities are crucial for ensuring operational safety and efficiency, where precise control and accurate data are paramount.
Subzero LNG Environment: Characteristics and Challenges
Liquefied natural gas (LNG) is natural gas that has been cooled to a liquid state at around -260°F (-162°C). This process transforms natural gas into a dense, energy-rich liquid, facilitating its storage and transportation. However, the extreme cold associated with LNG operations introduces several challenges for equipment used in these environments.
Extreme Temperatures
The primary challenge VT1000 in Subzero LNG Environment in a subzero LNG environment is managing the extremely low temperatures. These temperatures can cause materials to become brittle and affect the performance of electronic components. For the VT1000, this means that the device must be engineered to operate reliably despite the risk of thermal contraction and the effects of cryogenic conditions.
Safety Concerns
Safety is a major concern in LNG environments due to the potential hazards associated with cryogenic temperatures and the flammable nature of natural gas. Equipment must adhere to strict safety standards to prevent accidents and ensure safe operation. The VT1000’s design includes features aimed at mitigating these risks, such as thermal insulation and protective enclosures.
Thermal Stress
Thermal stress occurs when a material experiences rapid changes in temperature, which can lead to deformation or failure. The VT1000 addresses this challenge through the use of materials that can withstand thermal stress and mechanisms that accommodate temperature fluctuations without compromising the device’s integrity.
Performance of the VT1000 in Subzero Conditions
The VT1000’s performance in subzero LNG environments is a testament to its advanced engineering and design. Its ability to function effectively at extremely low temperatures is crucial for maintaining operational efficiency and safety in LNG facilities.
Temperature Tolerance
The VT1000 is designed to endure the extreme temperatures encountered in LNG environments. Its components are selected for their ability to retain strength and flexibility in cryogenic conditions. This ensures that the device can operate consistently without experiencing performance degradation due to the cold.
Material Selection
Material selection is a critical factor in the VT1000’s performance. The device is built using materials that are not only durable but also capable VT1000 in Subzero LNG Environment of withstanding the effects of extreme cold. This includes metals and composites that do not become brittle or lose their structural integrity at low temperatures.
Electronic Performance
Electronic components are particularly sensitive to low temperatures. The VT1000’s electronics are specifically designed and tested for cryogenic environments. This involves using components that maintain their functionality in extreme cold and integrating heating elements or insulation to keep critical electronics within operational temperature ranges.
Installation Considerations
Proper installation is crucial for ensuring the VT1000’s effective operation in LNG environments. The installation process involves several considerations to ensure that the device is correctly positioned and protected from extreme conditions.
Placement and Positioning
When installing the VT1000, it is important to choose a location that provides adequate protection from direct exposure to extreme cold. This may involve placing the device in a controlled environment or using protective enclosures to shield it from the harsh conditions of the LNG environment.
Thermal Insulation
Thermal insulation plays VT1000 in Subzero LNG Environment a vital role in maintaining the VT1000’s performance. Insulation helps to protect the device from the effects of extreme temperatures and ensures that its internal components remain within their operational temperature ranges. Proper insulation also helps to prevent thermal stress and potential damage to the device.
Mounting and Stability
For devices that are mounted or fixed in place, ensuring stability is essential. The VT1000 must be securely mounted to prevent movement or vibration that could affect its performance. Proper mounting also ensures that the device remains in the correct position, facilitating accurate measurements and control.
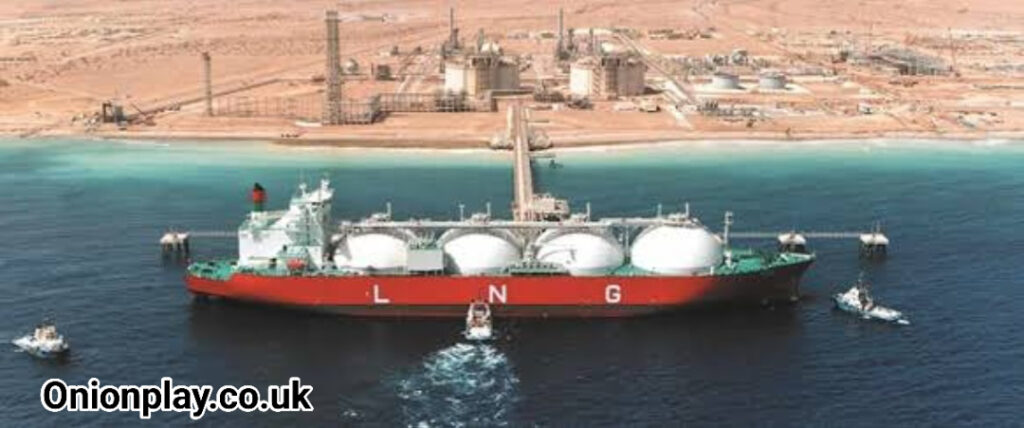
Maintenance and Upkeep
Regular maintenance is necessary to ensure the continued performance and reliability of the VT1000 in subzero LNG environments. Maintenance practices focus on keeping the device in optimal condition and addressing any issues that may arise due to the harsh conditions.
Routine Inspections
Routine inspections are essential for identifying signs of wear and tear or potential issues with the VT1000. Regular checks help to ensure that the device remains in good working order and that any problems are addressed before they impact performance.
Calibration and Testing
Periodic calibration and testing are crucial for maintaining the accuracy of the VT1000. In LNG environments, where precise measurements are critical, ensuring that the device is properly calibrated helps to maintain operational efficiency and safety.
Component Replacement
Over time, certain components of the VT1000 may experience wear or degradation. Replacing these components as needed ensures that the device continues to function effectively and reliably. This includes replacing any parts that may be affected by the extreme cold or other environmental factors.
Addressing Challenges and Implementing Solutions
The use of the VT1000 in subzero LNG environments presents several challenges, but effective solutions can address these issues and ensure optimal performance.
Managing Thermal Stress
Thermal stress can be VT1000 in Subzero LNG Environment mitigated through the use of thermal buffering mechanisms and materials designed to accommodate temperature fluctuations. The VT1000 is equipped with features that help to manage thermal stress and prevent damage due to rapid temperature changes.
Ensuring Electronic Reliability
Ensuring the reliability of electronic components in cryogenic conditions involves using specialized components that are tested for extreme cold. The VT1000’s electronics are designed to function correctly in low temperatures, and additional measures such as heating elements help to maintain operational temperatures.
Enhancing Safety
Safety in LNG environments is addressed through the integration of safety features in the VT1000’s design. This includes protective enclosures, thermal insulation, and adherence to safety standards to prevent accidents and ensure safe operation.
Real-World Applications
The VT1000’s ability to perform reliably in subzero LNG environments makes it a valuable tool in various industrial applications. Its use in LNG plants, transportation, and storage highlights its versatility and effectiveness.
LNG Plants
In LNG plants, the VT1000 is used for monitoring and controlling various processes. Its precision and reliability are crucial for maintaining smooth operations and ensuring safety in these high-stakes environments. The device’s ability to operate in extreme cold helps to ensure that LNG processes run efficiently and safely.
Transportation and Storage
The VT1000 also plays a role in the transportation and storage of LNG. Accurate monitoring and control are essential for managing the complexities of handling liquefied natural gas. The device’s robustness and performance in cold conditions contribute to effective management of LNG during transport and storage.
Conclusion
The VT1000 represents a significant advancement in technology designed to operate effectively in subzero LNG environments. Its robust design, precise functionality, and ability to withstand extreme temperatures make it an invaluable tool in the LNG industry. Understanding its dimensions, installation requirements, and performance capabilities provides insights into how this device contributes to operational efficiency and safety in challenging conditions.
By addressing the challenges of thermal stress, electronic reliability, and safety, the VT1000 demonstrates its suitability for use in the harsh environment of liquefied natural gas operations. Its real-world applications in LNG plants and transportation further highlight its importance and effectiveness.
As industries continue to operate in increasingly demanding conditions, technologies like the VT1000 play a crucial role in ensuring that equipment performs reliably and efficiently. The insights gained from examining the VT1000’s performance in subzero LNG environments underscore the importance of advanced engineering and design in meeting the needs of modern industrial applications.
Also read this: disappearing-dining-rooms